پوششهای مقاوم دربرابر حریق انواع مختلفی دارند. در این مقاله از سایت اخگر بنا این پوششها را به خوبی بررسی می کنیم.
پوشش های مقاوم در برابر حریق سازه:
1- طراحی ضخامت پوشش مقاوم در برابر حریق:
رایج ترین نحوه محاسبه در ایران استفاده از نسبت سطح آتش خور المان به سطح مقطع المان است.
: محیط سطح آتش خور فلزHp
: سطح مقطع المانA
نکته 1: برای تیرها بصورت 3 وجهی و برای ستونها بصورت 4 وجهی محاسبات انجام میشود.
نکته 2: دمای بحرانی برای تیرها 620 درجه و برای ستونها 620 درجه در نظر گرفته شود.
نکته 3: شرکتهای تامین کننده مصالح مقاوم در برابر حریق با توجه به انجام آزمایشات زیر نظر مرکزتحقیقات، راه، مسکن وشهرسازی گواهینامه ای از سوی مرکز اخذ نموده که برای هر شرکت جدول ضخامت متفاوتی وجود دارد.
2-اجرای پوشش ضدحریق با استفاده از محصول نفتکو
1- اخذ پرمیت و دریافت نقشه های اجرائی:
اخذ پرمیت از کارفرما جهت شروع عملیات پوشش مقاوم در برابر حریق اسکلت فلزی.
2- داربست بندی:
ابتدا برای مکان هایی که نیاز به اجرای پوشش ضد حریق دارند و در دسترس نیستند می بایست اقدام به اجرای داربست نمایید. (رعایت اصول ایمنی در این مورد بسیار مهم است.)
3- زیر سازی:
مرحله اول، برداشتن زنگ های احتمالی سطح بوسیله کاردک، برس سیمی، Power Brush (کاسه برس) و ….. می باشد.
مرحله دوم، عاری نمودن سطح مورد نظر ( سازه ) از هرگونه خاک، روغن، چربی، گریس و باقی مانده گازوئیل …. که می بایست به وسیله شستشو سطح از بین بروند.
مرحله سوم، انجام عملیات سنگ زنی، پین کوبی و توری بندی است. در این مرحله از کار می بایست تمامی سطوحی که نیاز به پوشش ضد حریق دارند توسط توری مرغی به صورت زیر توری بندی گردند.
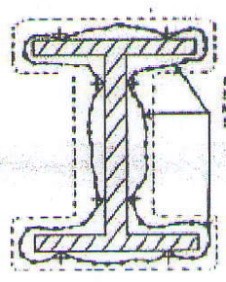
مرحله چهارم، انجام عملیات کاورینگ جهت جلوگیری از پاشش مواد اضافه برروی سطوح دیگر می باشد.
مرحله پنجم، در زمانی که از مواد پایه سیمانی ( نفکو ام دی و یا نفکو ال دی) برای سطح مورد نظر استفاده می شود می بایست قبل از اجرا از پرایمر Naftex PSA و یا پرایمر SBR به روش Key Coat استفاده شود.
ضمناً بعد از اجرای Key Coat )پرایمر (SBR و یا Naftex در شرایط عادی (دمای 20 درجه سانتی گراد و 50 درصد رطوبت) می بایست صبر نمود تا Key Coat )پرایمر (SBR و یا Naftex خشک گردد سپس مواد با پایه سیمانی را اجرا نمود.(این زمان با توجه به شرایط محیط تعیین می گردد و در شرایط عادی در حدود 6 الی 8 ساعت می باشد.)
4- آماده سازی دستگاه ها جهت پاشش متریال ضد حریق :
در این مرحله نیاز است تا دستگاه های زیر جهت اجرای عملیات پاشش مواد ضد حریق آماده گردند.
دستگاه کمپرسور:
این دستگاه جهت تامین هوای مورد نیاز سر نازل پاشش و همچنین اجرای عملیات مورد استفاده قرار می گیرد. ضمنا جهت کنترل نمودن فشار هوای کمپرسور باید از یک رگلاتور که برروی شیر خروجی هوای دستگاه بسته می شود استفاده نمود.
جهت اجرای مواد ضد حریق فشار هوای خروجی این دستگاه باید در بازه 20 تا 25 psi تنظیم گردد تا جائی که مانع فعالیت پاششکار نگردد. کاهش و یا افزایش فشار هوا هیچ اثری روی برونده (دبی خروجی) متریال نداشته و فقط وزن مخصوص و مصرف متریال را بالا می برد (مثال لوبیا و ماش).
برونده متریال تنها تابع رگلاژ نمودن پکینگ دستگاه پاشش می باشد. لازم است جهت جلوگیری از خرابی، دستگاه دورتر از مکانی که عملیات پاشش در آنجا صورت می گیرد قرار گیرد تا از مکش مواد به داخل کمپرسور و ایجاد صدمات به آن جلوگیری به عمل آید. همچنین باید روغن دستگاه روزانه و فیلتر هوای کمپرسور هفتگی چک گردد.
دیگ رنگ:
این دستگاه جهت اجرای پرایمر مورد استفاده قرار می گیرد که لازم است بعد از اجرای پرایمر با آب شستشو گردد. شیلنگ دستگاه نیز کاملا با آب تمیز گردد تا از مسدود شدن توسط پرایمر جلوگیری گردد.
دستگاه پاشش ( Mixer ) یا خلاطه:
این دستگاه شامل میکسر و مخزن پمپ مواد می باشد. لازم به ذکر است که این دستگاه در دو نوع بدون کمپرسور هوا ( یک تکه ) که روی خود دستگاه پاشش نصب می باشد و با کمپرسور هوا ( دو تکه ) که جدا از دستگاه پاشش است ساخته شده است. ضمنا جهت کنترل نمودن فشار هوای کمپرسور باید از یک رگلاتور که برروی شیر خروجی هوای دستگاه بسته می شود استفاده نمود.
5- اختلاط مواد و شروع عملیات پاشش:
متریال پایه سیمانی ( نفکو ام دی و ال دی )Nafco MD & LD
نفکو ام دی و ال دی در بسته های 20 کیلوگرمی ارائه می شود و دارای دانسیته ای حدود420 تا 520 kg/m³ می باشد .
در هنگام مخلوط نمودن نفکو ام دی با آب و همچنین پاشش آن باید به نکات زیر توجه نمود:
ابتدا حدود 14 لیتر آب قابل شرب داخل میکسر بریزید. سپس یک بسته از نفکو ام دی را داخل دستگاه می ریزیم. حال در حالی که میکسر روشن است کم کم در حدود 14 الی 18 لیتر آب قابل شرب دیگر به مواد اضافه می کنیم. بنابراین در مجموع حدود 26 الی 30 لیتر آب به نفکو ام دی اضافه می شود.
فرآیند اختلاط در حدود 5/2 الی 5/3 دقیقه ادامه می یابد. سپس دریچه پائین میکسر را باز کرده تا مواد داخل مخزن پمپ دستگاه ریخته شود. (این حجم آب می بایست به صورت تجربی در کارگاه تست شود.) بهتر است علی الخصوص در فصول سرد سال دمای آب در حدود 25 الی 35 درجه سانتیگراد باشد.
در هنگام پاشش نیز پاششکار باید به این نکته توجه داشته باشد که مواد را بر روی هم و با فشار پاشش ننماید چرا که فشار زیاد هوا و همچنین انباشته شدن مواد بر روی هم سبب هدر رفتن متریال می گردد.
در مورد نفکو ام دی دانستن نکات زیر الزامی می باشد:
1- متریال نفکو ام دی می تواند تا مدت 12 ماه پس از تولید مصرف گردد.
2- قطر داخلی شیلنگ هوای کمپرسور نباید کمتر از “8/3 (10 م م ) باشد.
3- کیسه های نفکو ام دی را نباید روی زمین و در کنار دستگاه میکسر قرار داد . (در جای خشک و دور از هرگونه رطوبت قرار گیرد.)
4- PH سیمان ، قلیائی (12) می باشد لذا می بایست به این نکته توجه نمود که این ماده با بعضی از پرایمرهای (رنگ ها) سازه فلزی همانند رنگ های سیلیکونی و آلکیدی که PH اسیدی دارند سازگار نبوده و با آنها واکنش می دهد. اما این مشکل با داشتن پرایمر Naftex که قبل از نفکو ام دی برروی سطح مورد نظر اجرا می شود، برطرف می گردد.
5- دمای آب شربی که می بایست با نفکو ام دی مخلوط گردد، بین 25 تا 35 درجه سانتیگراد است، که دمای 35 درجه برای مکان هائی که دارای هوا بسیار سرد می باشد بسیار با اهمیت است.
6- در زمان هائی که هوا سرد می باشد در هنگام اجرای نفکو ام دی می بایست منطقه اجرا را با استفاده از پلاستیک و یا برزنت محصور نموده تا از رد و بدل شدن هوای سرد در آن ناحیه جلوگیری بعمل آید.
7- برای اختلاط نفکو ام دی می بایست در ابتدا در حدود 14 لیتر آب شرب را داخل دستگاه میکسر بریزیم و سپس نفکو ام دی را ریخته و کم کم در حالی که میکسر روشن است بقیه آب شرب را وارد میکسر نمائیم. (در مجموع بین 26 الی 30 لیتر آب شرب نیاز است.) (این حجم آب می بایست به صورت تجربی در کارگاه تست شود.)
8- برای دستگاه های میکسر با 35 دور در دقیقه زمان اختلاط در حدود 5/2 الی 5/3 دقیقه می باشد.
9- فشار هوای خروجی از کمپرسور که به سر نازل پاشش انتقال می یابد، در حدود 30 الی 40 psi می باشد. (این فشار را به وسیله رگلاتور کنترل نمائید.)
10- فاصله دست پاششکار (نازل پاشش) تا سطح کار در حدود 30 الی 60 سانتی متر باید باشد. همچنین حرکت دست پاششکار نیز یک حرکت گردشی نرم از چپ به راست و عمود بر سطح باشد تا یک سطح صاف و منظم بعد از پاشش ایجاد گردد.
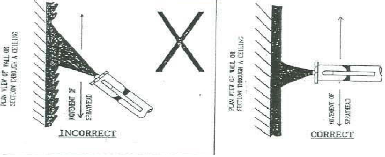
11- بهترین ضخامت پرایمر Naftex در زمان اجرا 100-125 میکرون (ضخامت تر) و 50-70 میکرون (ضخامت خشک) می باشد. بطور کلی این ضخامت تر باید در بازه 100-150 میکرون و ضخامت خشک در بازه 55-82 میکرون باشد.
توجه نمائید به هر نسبتی که Naftex را با آب رقیق می کنید به همان نسبت نیز می بایست ضخامت تر را زیاد نمائیم. در ضمن Naftex در مدت 6 الی 8 ساعت در شرایط دمائی استاندارد (20 درجه سانتیگراد و 50 درصد رطوبت) بطور کامل خشک می گردد.
12- اگر شرایطی پیش آمد که نفکو ام دی را در 2 بار پاشش بخواهیم اجرا نمائیم می بایست هر لایه (ضخامت 20 م م) را به مدت 2 تا 6 ساعت بعد در شرایط محیطی عادی (دمای 20 درجه سانتیگراد و 50 درصد رطوبت) اجرا نمود. اگر سطح مورد نظر پس از اجرای لایه اول خشک بود می بایست سطح را مرطوب نمائیم.
13- در شرایط دمائی کمتر از 4 درجه سانتیگراد و بیشتر از 50 درجه سانتیگراد نمیتوان پاشش را انجام داد. (ضمنا به این نکته نیز میبایست توجه داشت که علاوه بر دمای محیط، دمای سطح سازه نیز مهم است.)
14- شیلنگ پاشش بهتر است بصورت یک تکه باشد. در صورت نیاز و کار در ارتفاع با استفاده از کوپلینگ استاندارد یک شیلنگ دیگر اضافه گردد. (بهترین متراژ برای طول شیلنگ 8 متر می باشد.)
15- میتوان جهت انجام تعمیرات احتمالی سطحی به میزان 5/1 متر مربع را با استفاده از وسایل بنائی اجرا نمود.
را مد نظر قرار داد تا از اتلاف بیش از حد مواد و دیگر مشکلات احتمالی جلوگیری نمائید.
شرایطی که به زیبائی و تمیزی سطح کار پوشش ضد حریق نفکو ام دی و ال دی کمک می نماید:
• نازل پاشش عمود بر سطح کار باشد. (مغزی شماره 12 یا 14 استفاده شود)
• فشار هوای سر نازل تنظیم باشد.
• شیلنگ پاشش کوتاه ( استاندارد = 8 متر ) باشد.
• مدت زمان اجرای لایه اول به 2 الی 6 ساعت رسیده باشد و سپس لایه دوم را اجرا نمائید.
• اگر سطح لایه اجرا شده اول بطور کامل خشک بود می بایست سطح را کمی مرطوب نمود.
• قطر شیلنگ پاشش بیشتر از “1 (25 م م) باشد.
• از دستگاه های استاندارد استفاده شده باشد.
• میزان آب شرب مخلوط شده استاندارد باشد.
*** پس از اجرای عملیات پاشش، لازم است تا محوطه کار تمیز گردد ***
6- تاپ کت (آنتی رین):
جهت ماندگاری سیستم پوشش ضد حریق در شرایط محیطی می بایست از رنگ های سازگار با متریال پایه سیمانی نفکو ام دی و یا نفکو اچ دی برروی پوشش ضد حریق استفاده نمود. همچنین این رنگ ها حتما می بایست بر پایه آب بود و خاصیت تنفسی داشته باشند . ضخامت این نوع از رنگ ها نیز می بایست در حدود 30 الی 50 میکرون به صورت خشک باشد.
زمانی این رنگ باید اجرا گردد که متریال نفکو کاملا خشک باشد. این زمان در حدود 20 الی 30 روز پس از اجرای لایه نهایی متریال پایه سیمانی خواهد بود.(20 درجه سانتیگراد و 50 درصد رطوبت) تاپ کت انتخابی بوده و اجباری نیست و برای صنایع نفت و گاز و یا محیط های باز مورد استفاده قرار می گیرد. (بنا به نیاز کارفرمایان محترم)
7- درزگیر (ماستیک):
پس از اجرای آنتی رین در نقاطی که متریال پایه سیمانی با سطوح فلزی در تماس هستند، باید بدلیل جلوگیری از عبور آب به زیر متریال ضد حریق، تمامی آن نقاط توسط درزگیر مناسب درزبندی گردند. مناسب ترین درزگیر نیز ماستیک آکریلیک سیلیکونی می باشد. ماستیک برای صنایع نفت و گاز و یا محیط های باز مورد استفاده قرار می گیرد.
8- ضخامت سنجی:
روش ضخامت سنجی نیز بر اساس استاندارد ASTM E-605 می بایست به شرح زیر انجام گیرد.
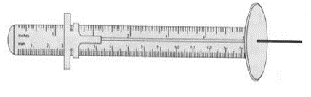
توجه:
تلرانس هر نقطه ضخامت سنجی تا منفی 6 میلیمتر ضخامت یا کمبود 25 درصد ضخامت قابل قبول است. البته به شرطی که میانگین ضخامت سنجی در یک المان معادل ضخامت طراحی باشد.
بهترین روش های پاشش نیز مطابق شکل های زیر می باشد:
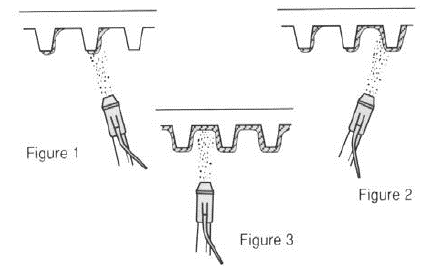
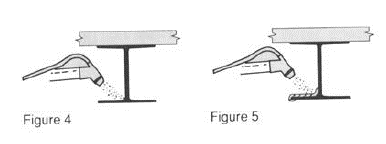
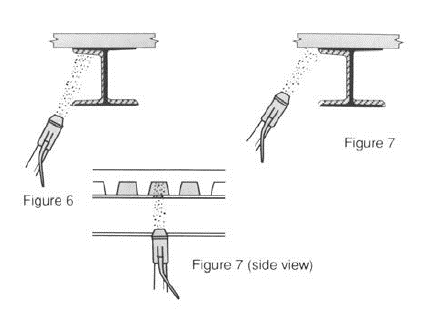
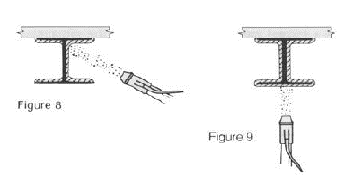