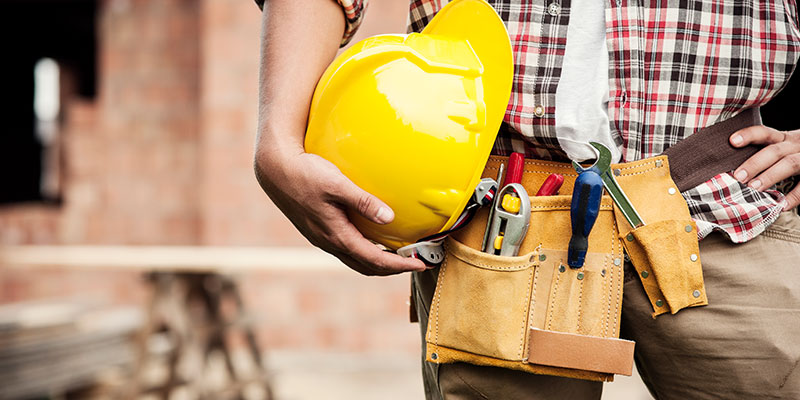
مقاوم سازی ساختمانها در برابر آتش
5 هدف اصلی برای تامین ایمنی در برابر آتش
از عوامل مهم در طراحی ساختمانها در برابر حریق ، محافظت در برابر آتش است.بنابراین ایمنی در برابر آتش با در نظرگرفتن دو هدف اصلی ایمنی جانی و مالی برای هر ساختمان مورد بررسی قرار میگیرد.
- طراحی مناسب مسیرهای خروج
- فضابندی مناسب ساختمان جهت جلوگیری از آتش
- پیشگیری
- شبکه های هشدار حریق
- پیش بینی وسایل مناسب دستی و خودکار
تقسیم بندی آتش از نظر منبع
سلولزی
این نوع حریق که حاصل سوختن مواد سلولزی میباشد، دما با گذشت حدود 1 ساعت به مرز بیش از 900 درجه سانتیگراد میرسد.(حریق سلولزی در ساختمانهایی همانند ساختمانهای مسکونی، اداری، بیمارستانها، مدارس و… رخ میدهد.)
هیدروکربنی
این نوع حریق به واسطه سوختن مواد شیمیایی و سوختهایی چون گاز یا سوختهای مایع در انبارهای شیمیایی و مراکز صنعتی و صنایع نفت و گاز و پتروشیمی ایجاد میشود.
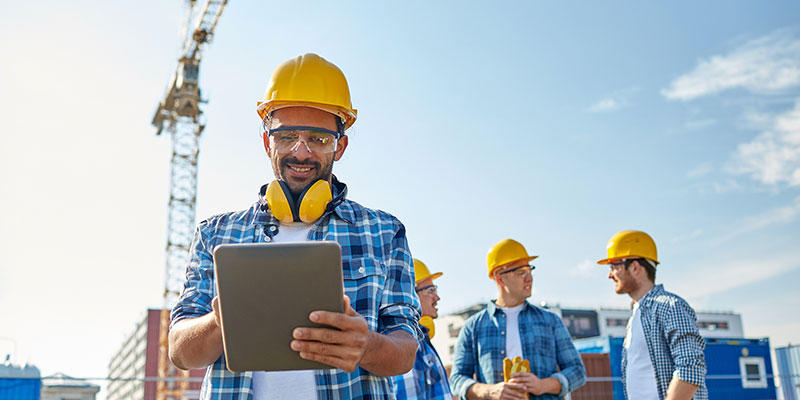
آیین نامه ها
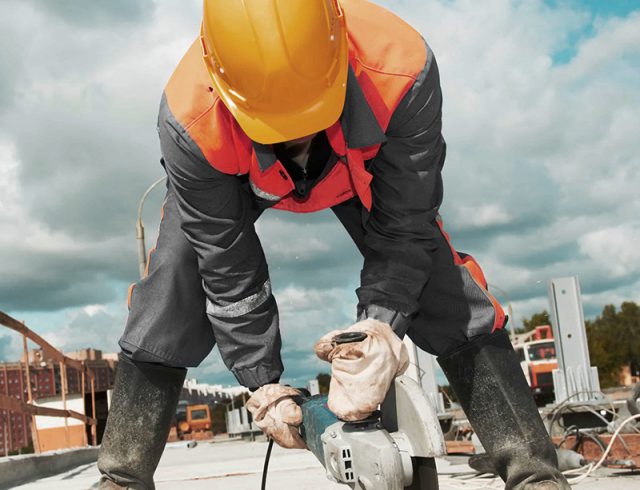
بین المللی
که از مهمترین آنها میتوان به سه آیین نامه ذیل اشاره نمود :
- Ineternational Building Code (IBC)
- National Fire Protection Association (NFPA)
- The Building Regulation Fire Safety
داخلی
که از مهمترین آنها میتوان به سه آیین نامه ذیل اشاره نمود.
- مبحث سوّم مقرّرات ملّی ساختمان
- نشریه 112
- نشریه 682
- نشریه 112
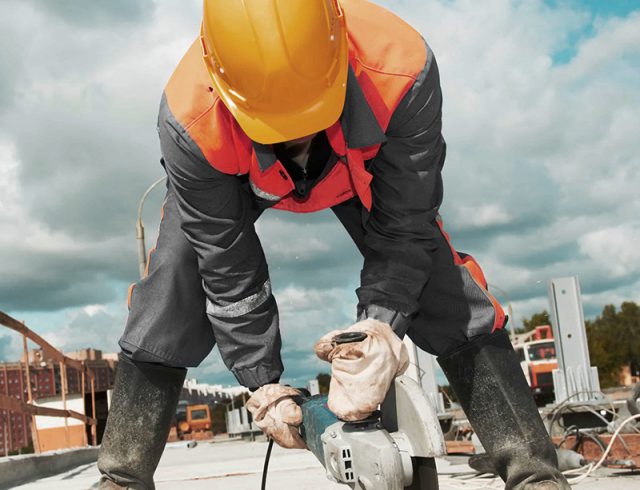
عوامل تعیین میزان مقاومت در برابر حریق
بررسی و تعیین میزان تصرفها در طبقات و نحوه جداسازی تصرفها
تعیین تصرفها بر اساس نقشههای معماری و کاربری
بررسی سیستم سازهای و ساختار و نیاز سنجی
بررسی تعاریف آئین نامه ای و خدمات مرتبط
بررسی محدودیتهای ارتفاع، مساحت و تعداد طبقات
تعیین میزان مقاومت مورد نیاز در برابر حادثه
مقاوم سازی
انواع روشهای محافظت در برابر حریق
معماری
سازه
تاسیسات مکانیکی و برقی
مقاوم سازی
انواع روشهای مقاوم سازی
غیرفعال
فعال
انواع سازه ها
مواد اسپری شوینده معدنی(سیمانی و گچی)
مواد اسپری شونده پف کننده(رنگ ضدحریق)
برد های تخت
مصالح بنایی
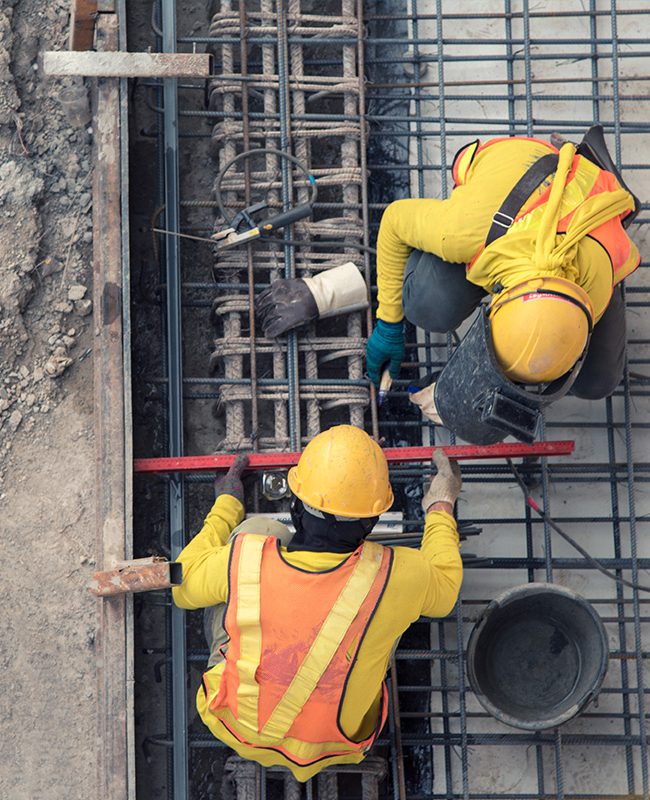
طراحی ضخامت پوشش مقاوم در برابر حریق
رایج ترین نحوه محاسبه در ایران استفاده از نسبت سطح آتش خور المان به سطح مقطع المان است. : Hp -1محیط سطح آتش خور فلز 2- A سطح مقطع المان .از عوامل مهم در طراحی ساختمانها در برابر حریق ، محافظت در برابر آتش است.بنابراین ایمنی در برابر آتش با در نظرگرفتن دو هدف اصلی ایمنی جانی و مالی برای هر ساختمان مورد بررسی قرار میگیرد.
نکته 1
برای تیرها بصورت 3 وجهی و برای ستونها بصورت 4 وجهی محاسبات انجام میشود.
نکته 2
دمای بحرانی برای تیرها 620 درجه و برای ستونها 620 درجه در نظر گرفته شود.
نکته 3
شرکتهای تامین کننده مصالح مقاوم در برابر حریق با توجه به انجام آزمایشات زیر نظر مرکزتحقیقات، راه، مسکن وشهرسازی گواهینامه ای از سوی مرکز اخذ نموده که برای هر شرکت جدول ضخامت متفاوتی وجود دارد.
اجرای پوشش ضدحریق با استفاده از محصول نفتکو
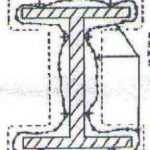
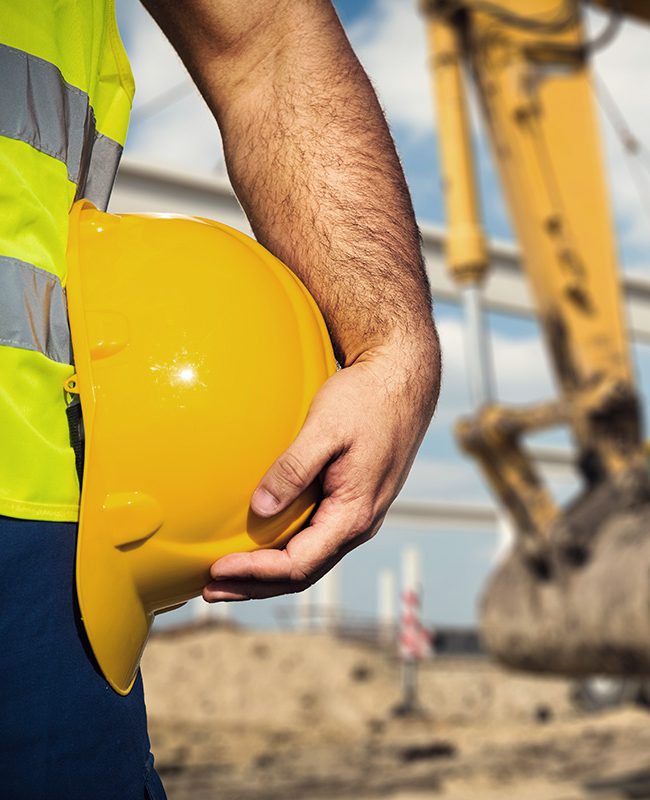
آماده سازی دستگاه ها جهت پاشش متریال ضد حریق
در این مرحله نیاز است تا دستگاه های زیر جهت اجرای عملیات پاشش مواد ضد حریق آماده گردند . دستگاه کمپرسور : این دستگاه جهت تامین هوای مورد نیاز سر نازل پاشش و همچنین اجرای عملیات مورد استفاده قرار می گیرد . ضمنا جهت کنترل نمودن فشار هوای کمپرسور باید از یک رگلاتور که برروی شیر خروجی هوای دستگاه بسته می شود استفاده نمود. جهت اجرای مواد ضد حریق فشار هوای خروجی این دستگاه باید در بازه 20 تا 25 psi تنظیم گردد تا جائی که مانع فعالیت پاششکار نگردد و کاهش و یا افزایش فشار هوا هیچ اثری روی برونده (دبی خروجی) متریال نداشته و فقط وزن مخصوص و مصرف متریال را بالا می برد (مثال لوبیا و ماش) و برونده متریال تنها تابع رگلاژ نمودن پکینگ دستگاه پاشش می باشد. لازم است جهت جلوگیری از خرابی ، دستگاه دورتر از مکانی که عملیات پاشش در آنجا صورت می گیرد قرار گیرد تا از مکش مواد به داخل کمپرسور و ایجاد صدمات به آن جلوگیری به عمل آید و همچنین روغن دستگاه روزانه و فیلتر هوای کمپرسور هفتگی چک گردد. دیگ رنگ : این دستگاه جهت اجرای پرایمر مورد استفاده قرار می گیرد که لازم است بعد از اجرای پرایمر با آب شستشو گردد و شیلنگ دستگاه نیز کاملا با آب تمیز گردد تا از مسدود شدن توسط پرایمر جلوگیری گردد . دستگاه پاشش ( Mixer ) یا خلاطه : این دستگاه شامل میکسر و مخزن پمپ مواد می باشد ، لازم به ذکر است که این دستگاه در دو نوع بدون کمپرسور هوا ( یک تکه ) که روی خود دستگاه پاشش نصب می باشد و با کمپرسور هوا ( دو تکه ) که جدا از دستگاه پاشش است ساخته شده است . ضمنا جهت کنترل نمودن فشار هوای کمپرسور باید از یک رگلاتور که برروی شیر خروجی هوای دستگاه بسته می شود استفاده نمود.
– اختلاط مواد و شروع عملیات پاشش
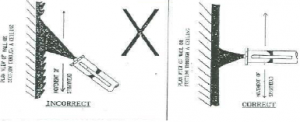
- نازل پاشش عمود بر سطح کار باشد. (مغزی شماره 12 یا 14 استفاده شود)
- فشار هوای سر نازل تنظیم باشد.
- شیلنگ پاشش کوتاه ( استاندارد = 8 متر ) باشد.
- مدت زمان اجرای لایه اول به 2 الی 6 ساعت رسیده باشد و سپس لایه دوم را اجرا نمائید.
- اگر سطح لایه اجرا شده اول بطور کامل خشک بود می بایست سطح را کمی مرطوب نمود.
- قطر شیلنگ پاشش بیشتر از “1 (25 م م) باشد.
- از دستگاه های استاندارد استفاده شده باشد.
- میزان آب شرب مخلوط شده استاندارد باشد.
- *** پس از اجرای عملیات پاشش ، لازم است تا محوطه کار تمیز گردد ***
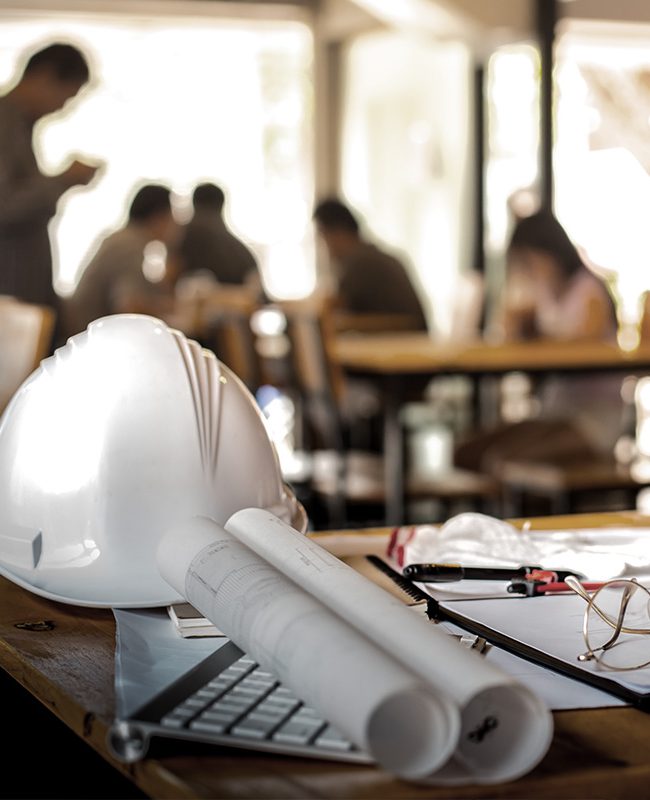
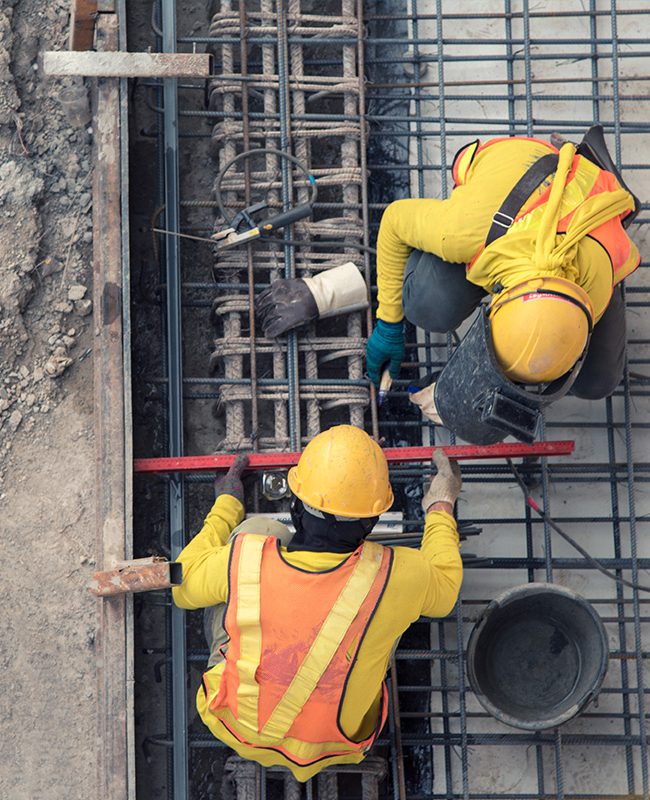